Material handling has been transformed in all industries around the world by automation. To further improve a company’s efficiency, productivity and cost effectiveness, integration of automated systems in material handling has moved from a nice to have to a must have. Material handling includes transportation, warehousing, control and guarding of materials and products during the production, warehousing and distribution chain. Historically these functions require significant human input and manual work with results of inefficiency, errors and liability. But automation has brought in a new era of accuracy, speed and reliability.
Increased Efficiency and Productivity
Biggest potential of automation in material handling is its high level of increased efficiency and productivity. Automated systems work at a constant rate without pauses, fatigue or human errors. Compared to manual work which can be inaccurate and labour intensive, robots and automated conveyors can do repetitive tasks fast and accurately. This throughput enables companies to put out orders faster, respond to customer needs faster and optimize the overall workflow.
Automated storage and retrieval systems (AS/RSs) and robotic arms in warehouses allow providers to pick and stack goods easily. AGVs can move materials around the installation site without human intervention, reducing the downtime in production and providing a continuous flow of production line. Plus with AI powered warehouse management systems, inventory management, order fulfilment and space are optimized which will help build a more productive and efficient supply chain.

Cost Savings and Long Term Profitability
Although the upfront cost of automation can be high, the ongoing cost savings makes it a cost effective investment for many companies. Automating agents reduces the need for human labour and thus saves labour cost. Companies can reassign human workers to higher level cognitive and implement specialized materials handling solutions rather than routine physical work tasks. This in turn increases not only employee satisfaction but also the potential of the workforce, i.e. ability to learn and adapt. Automation also reduces errors related to material movement, the cost of which is significant in terms of lost inventory, damaged goods and operational downtime. Automatic positioning and scanning devices ensure accurate inventory control, minimizing waste and overstocking or over-inventory.
Workplace Safety
Workplace safety is one of the biggest issues in industries where there is heavy lifting, hazardous materials or repetitive manual work. Automation reduces safety by reducing human involvement in dangerous activity. Robotic arms and conveyors are automated and can move heavy things without injuries related to lifting, bending and carrying. AGVs move around industrial environment without human intervention thus reducing incidents caused by human error or fatigue. Plus automation reduces exposure of workers to hazardous environment such as extreme temperatures, toxic substances or high risk machinery.
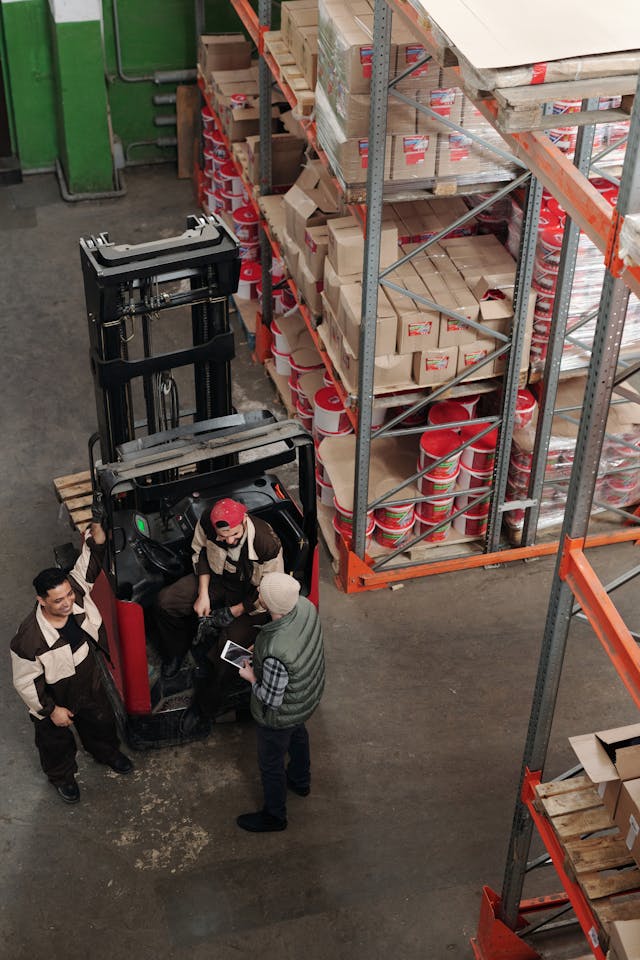
Integration Challenges and High Upfront Costs
Despite many benefits, automating material handling has its challenges especially during the initial stages. One of the biggest is the cost of buying and deploying the automated system. Medium and small enterprises (SMEs) may find it hard to purchase the expensive robotics, AI-based software and the infrastructure required for automation. Moreover, integrating automation into existing operations requires a lot of planning and modifications to warehouse layouts, production lines and supply chain processes.
Workforce Adjustment and Skills Requirements
Automating material handling presents concerns on workforce adjustment and future skills requirements in the industry. Although automation reduces manual work, demand for highly skilled workers to control, maintain and repair automated systems arises. How and if employees will be trained to use these new technologies such as robotics programming, data analysis, machine learning application is a key aspect of managing the automated process. Many workers will have to move from task-oriented to technology-oriented work and this can be difficult for them requiring companies to have training and up-skilling programs. Another point of concern is job displacement since automation will eliminate some roles that were historically occupied by human labour.